How to Get Started in
Space Robotics
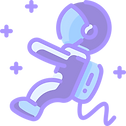
Robotics is an exciting and rapidly evolving field. For those with a keen interest for space, space robotics offers a unique opportunity to contribute to missions beyond Earth. Space robotics involves designing, programming, and developing robots that can operate in the harsh, unpredicatable environment of space - whether they’re helping astronauts in low Earth orbit, exploring distant planets, or supporting emerging industries like in-orbit servicing and manufacturing (IOSM). Let’s dive into how you can get started on your journey to become a space robotics engineer!
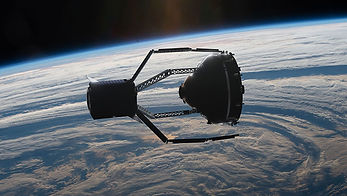


Robotics Fundamentals Still Apply
If you’re already familiar with general robotics, you’re ahead of the game! Core skills like:
-
Programming
-
Simulation
-
Mechanical design and kinematics
-
Electronics, sensor integration, and assembly
-
Control systems
are all transferable to space robotics. The difference lies in adapting these skills to be suitable to answer the unique challenges of space.
The Unique Challenges of Space Robotics
Space is an extreme environment that introduces many challenges for robots. These heavily influence how robots are deigned and how they operate. Here are some unique challenges for space:
-
Microgravity: Space is a vacuum with no gravity, this affects how robots operate and their kinematics. Without friction and stability, if the robot makes a wrong movement, this could lead to them drifting or colliding with another spacecraft. Robots need precise control mechanisms and stabilisation.
-
Intense radiation: Cosmic rays and solar radiation pose significant threats to the electronics and degrading materials over time. Radiation-hardened systems and shielding are crucial to ensure long-term functionality. NASA’s Perseverance Rover on Mars uses radiation-hardened systems for its electronics to survive the Martian surface.
-
Extreme temperature fluctuations: Space robots face extreme temperature fluctuations - shift from -173°C to +127°C on the Moon for example. In-orbit robots must also deal with rapid transitions between sunlight and shaded sides of the Earth or of their spacecraft. Internal thermal control systems such as coatings, Multi-Layer Insulation (MLI), and MEMS-based heat pipes are essential. The James Webb Space Telescope relies on a sunshield to keep its instruments at cryogenic temperatures.
-
Debris: Space debris pose collision risks. Low Earth Orbit (LEO) is crowded with thousands and thousands of pieces of space debris, from defunct satellites to small fragments of metal. Even tiny pieces of debris, travelling at high velocities, can cause severe damage to robotic systems and its spacecraft. For example, Canadarm2 on the International Space Station (ISS) was struck by a small piece of space debris in 2021, leaving a hole in its thermal blanket, yet it continued to function due to its durable design.
-
Limited power availability: For planetary missions, robots rely on solar panels for power but this energy is limited and can’t be collected during shadowed phases. As for robots on spacecraft, their challenge is that spacecraft are not designed (yet) to accomodate high-power needs for robots. For example, the Canadarm use on the ISS operates with such low power that it couldn’t lift itself in Earth’s gravity. This constraint to design highly efficient systems that are lightweight and maximise performance with minimal energy consumption.
-
Dust: On planetary surfaces, such as Mars or the Moon, dust can pose significant challenges. Fine particles can clog mechanical parts, interfere with sensors, or coat solar panels.
-
Vibration and Shock during launch: Robots must survive the intense vibration and shock forced during launch. These can damage joints and electronics and can leave your robot unusable. Robust engineering and extensive pre-flight testing are required.
-
Communication Delays: Communication from Earth often experience significant delays or can be unreliable. If your robot is in LEO, you only have a short 15 min window for every 2 hours to communicate with it. This means your robot needs advanced autonomy to complete tasks.
Materials and Design Considerations
Space robotics need lightweight yet durable materials. Traditional materials like steel may be too heavy, while composites and alloys like titanium or aluminum are commonly used. Additionally, robots must be resistant to vacuum conditions, avoiding materials that can outgas or degrade. NASA's Perseverance Rover uses titanium for critical components, balancing durability with weight reduction. Its wheels are made from a specialised aluminum alloy to handle the rough Martian terrain while remaining lightweight.
Understanding the Market
In-orbit servicing and manufacturing (IOSM) is one of the most exciting emerging fields for space robotics. IOSM refers to the ability to repair, upgrade, refuel, or assemble spacecraft while in orbit. This would extend the lifespan of satellites, reduce space debris, and enable new missions that would otherwise be impossible. According to the satellite tracking website Orbiting Now, as of April 18 2024, there are 9,822 active satellites orbiting our planet, along with 2,770 inactive objects. These numbers highlight the growing need for IOSM to manage satellites and prevent further debris in space:
-
Satellite servicing: Refueling, repairing, or replacing parts on satellites already in orbit. A great example is NASA’s OSAM-1 mission, which will demonstrate robotic satellite servicing by refueling a live satellite in space.
-
In-orbit assembly: Constructing large structures in space, like space stations, telescopes, or solar power plant. The SPIDER mission, part of the OSAM-2 program, is one such example, where a robotic arm will assemble large antennas in space.
-
Asteroid and Planetary mining: Extracting valuable resources like metals and rare minerals.
-
Planetary Exploration: Robots like NASA's Perseverance Rover are crucial in exploring the Martian surface, gathering scientific data, and performing scientific experiements.
-
Building Infrastructure: Building habitats as humanity aims for long-term missions to the Moon, Mars, and beyond. For example, NASA's Artemis program is looking at using robots for building lunar bases.
-
Debris removal: Capturing and removing defunct satellites and space debris. ClearSpace-1 mission by ESA will use a robotic arm to capture and deorbit space debris, marking a critical advancement in space debris management.
With IOSM, the need for autonomous, reliable, and capable robots is greater than ever. Engineers entering this field should focus on technologies like manipulation, autonomous navigation, and design.
Space Robotics Standards
While NASA’s safety and requirements standards, along with ESA’s guidelines, provide a solid foundation for space missions, specific standards for space robotics are still underdeveloped. There are established frameworks for reliability, safety, and some operational procedures, but there is little formalisation in areas crucial to robotics, such as data protocols, communication types, or interoperability between systems. This means that robotic technologies are often custom-built for individual missions, with little ability to seamlessly integrate across different platforms or agencies. As space robotics continues to grow, there’s a clear need for international collaboration to establish uniform standards in these areas.
Get familiar with the Lingo
When working in the space industry, you will need to be familiar with common words - general, engineering, business, mission, scientific, and legal. Here is a short dictionary.
General Terms
-
Launch Window: Time during which a spacecraft must be launched to reach its target.
-
Payload: The cargo carried by a spacecraft, like satellites or robots.
-
Orbit: Path a spacecraft or satellite follows around a celestial body.
-
Constellation: Group of satellites working together for the same mission.
-
Telemetry: Data transmitted from a spacecraft to Earth for monitoring and control.
-
In-Orbit Servicing and Manufacturing (IOSM): Activities involving the repair, refueling, or upgrading of satellites and spacecraft while in space. And manufacturing strucutres in space. In US, they use the term ISAM with A for assembly, such as assembling large antennas in space.
Engineering Terms
-
GNC: Guidance, Navigation, and Control systems. They are responsible for directing a spacecraft to its destination and mainting stability.
-
AOCS: Attitude and Orbit Control System. Used for controlling the position and orientation of spacecraft.
-
CubeSat: Mini satellite with standard one U dimension (10 x 10 x 10 cm), often used in LEO missions.
-
Bus: The part of a satellite that supports payloads, including power, communication, and propulsion systems.
Mission & Operational Terms
-
LEO: Low Earth Orbit, between 160 to 2.000 km alititude. Contains 84% of the active satellites as of May 2024. Low orbits are easier to reach and have certain advantages for small satellites. Radio signals take much less time to reach LEO than GEO.
-
MEO: Medium Earth Orbit, between 5.000 to 12.000 km altitude. Contains 3% of the active satellites as of May 2024.
-
GEO: Geostationary Earth Orbit. A circular orbit 35.786 km above Earth’s equator, where a satellite appears stationary relative to the Earth. Contains 12% of the active satellites as of May 2024.
-
Interplanetary Mission: Aimed at exploring or studying other planets within our solar systems.
-
Launch Vehicle: Rocket used to carry a spacecraft or satellite into space.
Business & Market Terms
-
NewSpace: Refers to the emergence of the private space industry. Focus on commercial ventures and innovations.
-
COTS: Commercial Off The Shelf. Ready made products used in space systems.
-
Dual Use Technology: Tech applicable to both civilian and military uses in space.
Scientific Terms
-
Microgravity: Condition in space where gravity is very small.
-
Radiation Hardening: Techniques to make electronic components resistant to damage from cosmic radiation.
Legal & Regulatory Terms
-
SAA: Space Act Agreement. A leal agreement that allows NASA to pertner with private companies.
-
ITAR: International Traffic in Arms Regulations. US export control laws governing sensitive defence-related technologies, including some space technologies.
Further Learnings
-
Learn about space systems in more depth: Space Mission Engineering
-
On Orbit Servicing, Assembly, and Manufacturing by the European Space Policy Institute
-
OSAM State of Play by NASA
-
NASA Robotics Alliance Project: provides students with opportunities to engage in robotics through hands-on experience, internships, and challenges designed to inspire careers in space robotics.
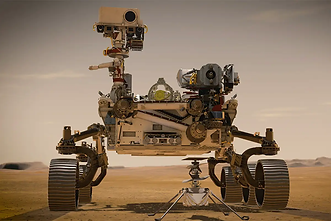

.png)



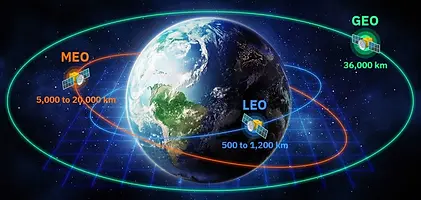

I would love to hear your feedback on this guide and what you would want to hear next! Please let me know HERE